クルマの企画・開発~生産まで
喜びと感動をお届けするクルマづくり
トヨタ車体では、商用バン、ミニバンの企画・開発~生産までを一貫して担っています。お客さまの暮らしを豊かにする、笑顔につながるクルマをお届けしたい。そのために、グローバルでの使われ方を知り、未来を描いたクルマづくりを行っています。
企画
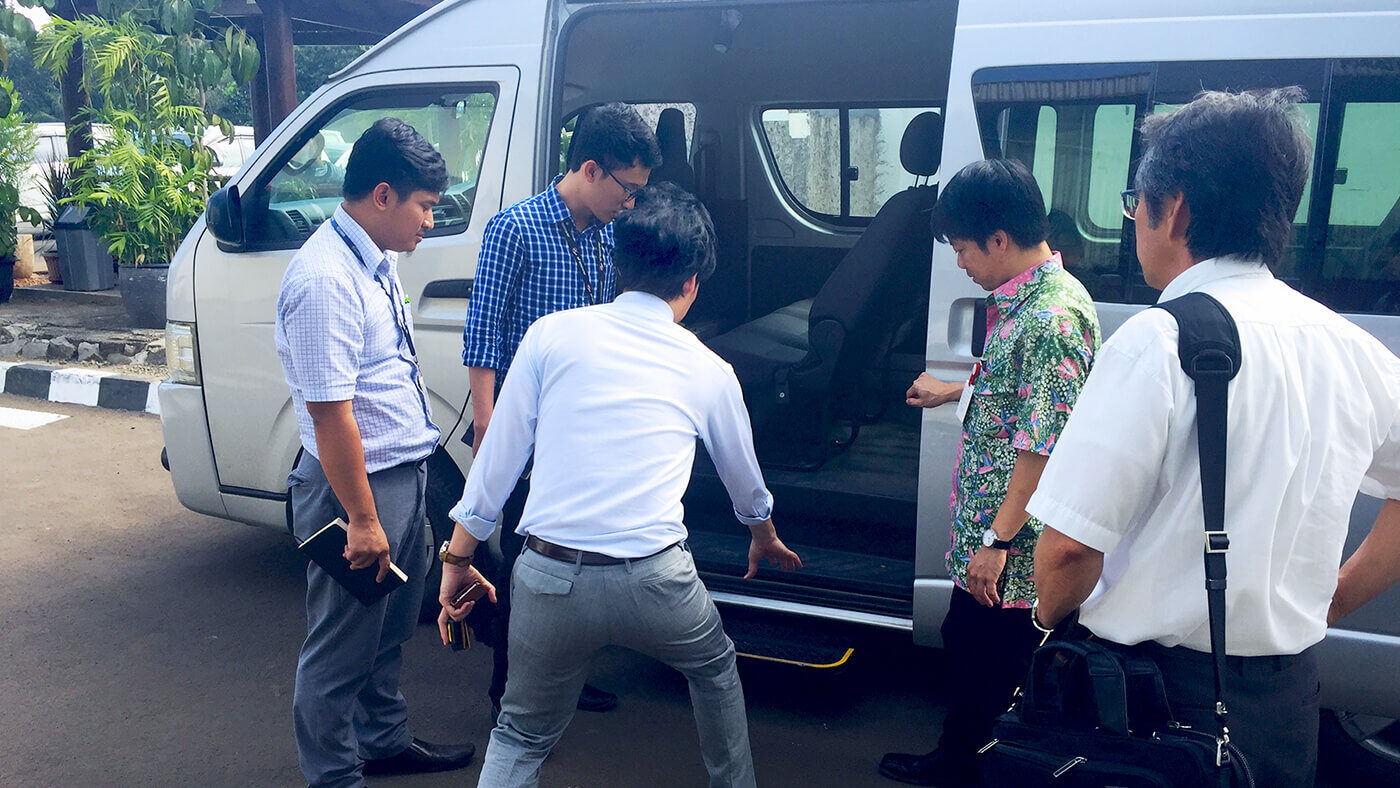
多くの国で使われているクルマだからこそ、その国にあった最適なクルマは何かを考え、コンセプトを練り上げます。
同じクルマでも地域や国によって使われ方は様々です。現地に出向き、使われ方を見て、お客様の声を聞き、もっといいクルマの企画につなげています。
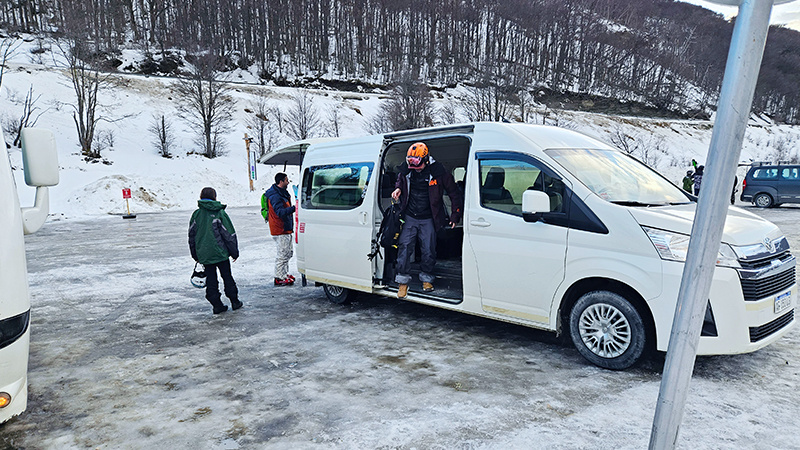
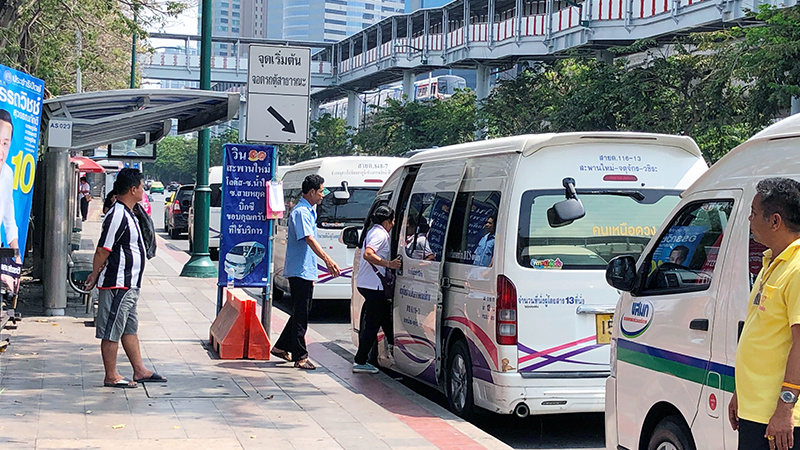
デザイン
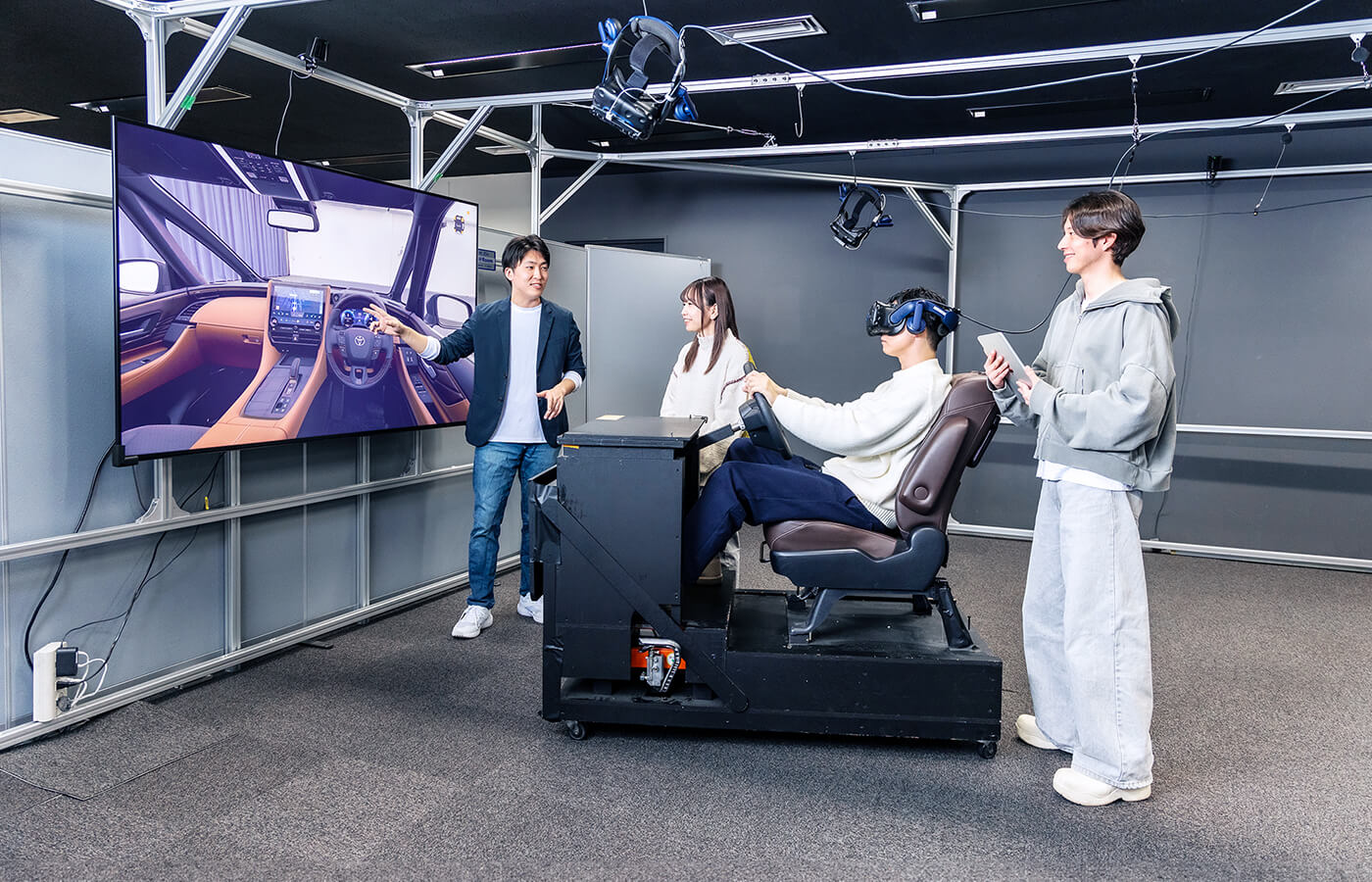
つくるクルマの企画がまとまったら、0からカタチにしていきます。お客様の笑顔を思い浮かべ、理想のクルマをカタチづくっていきます。
数案にしぼりこまれたアイデアを、3D映像や粘土(ねんど)で立体的につくるクレイモデルにして、1案にしぼり、最終デザインへと仕上げていきます。
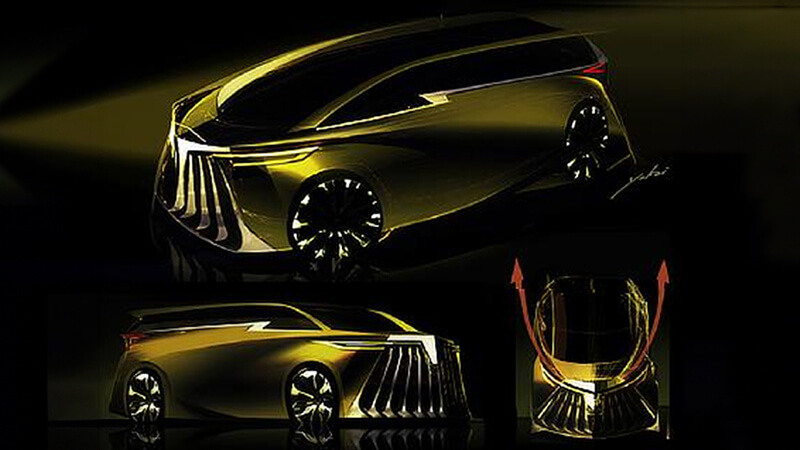
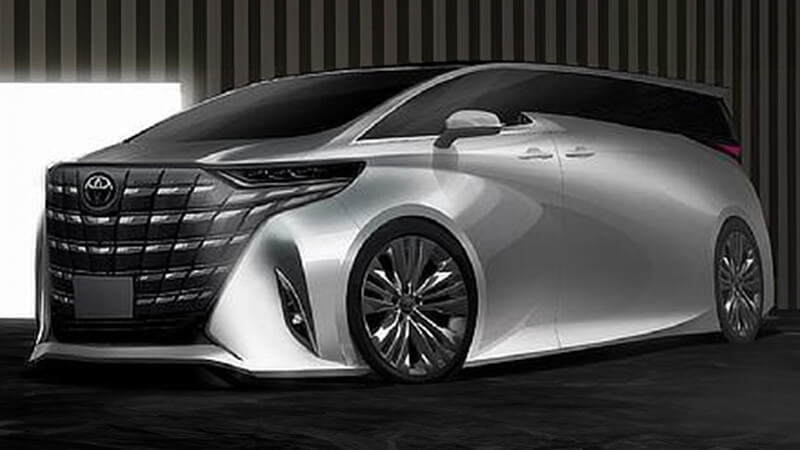
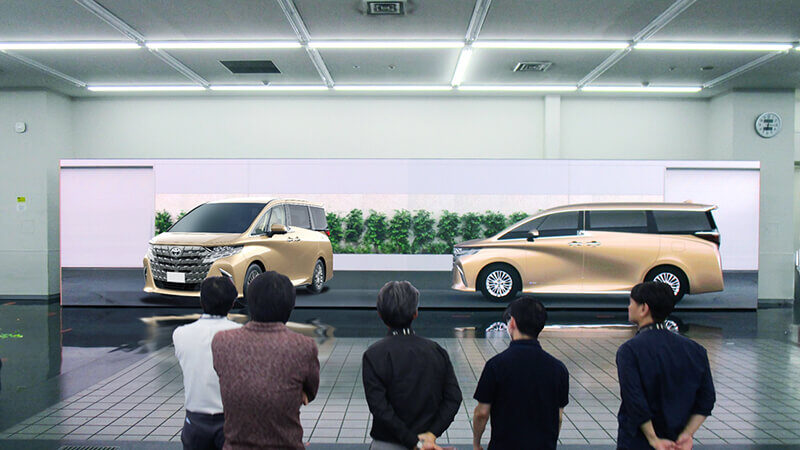
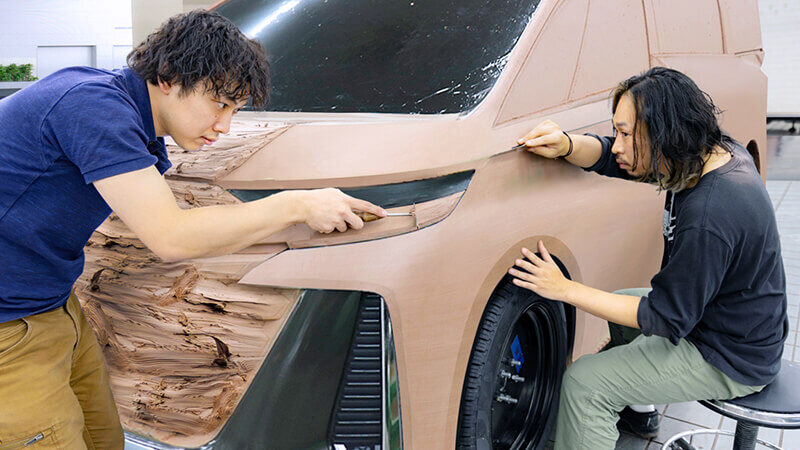
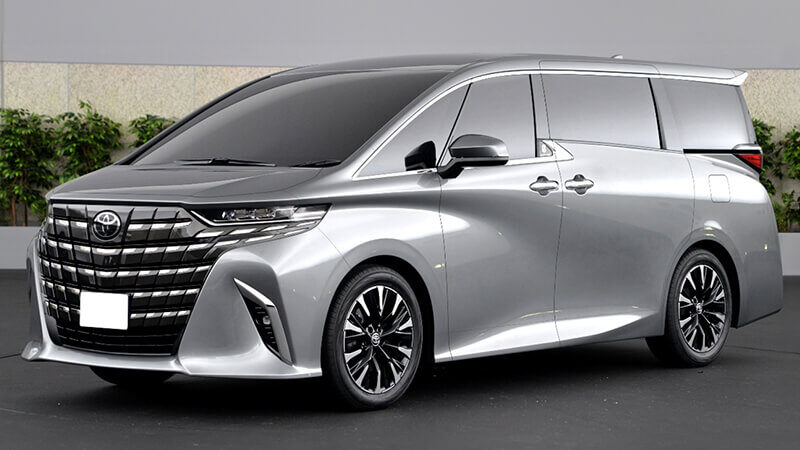
設計
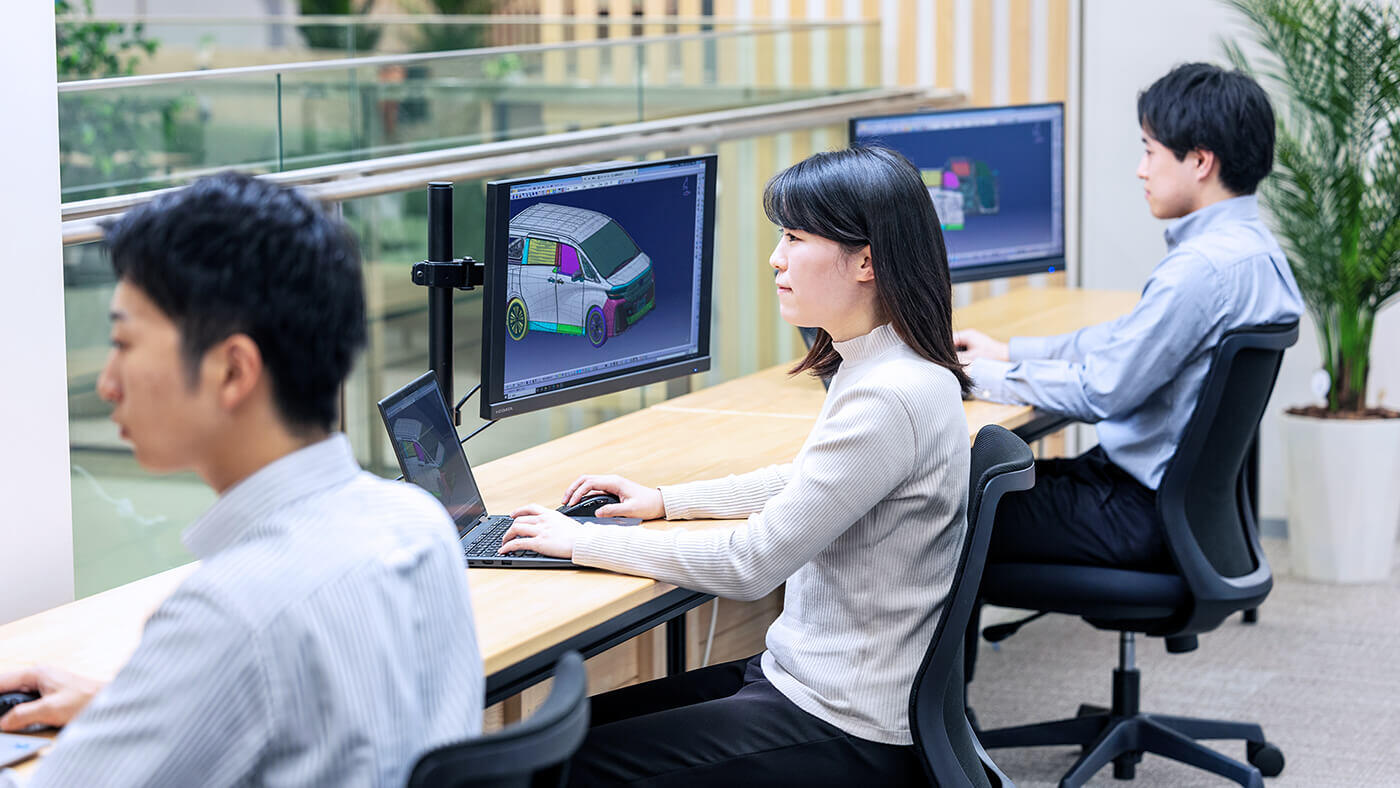
決定したデザインをもとに、乗り心地、乗り降りのしやすさ、つくりやすさなどを全体最適でつくりあげます。
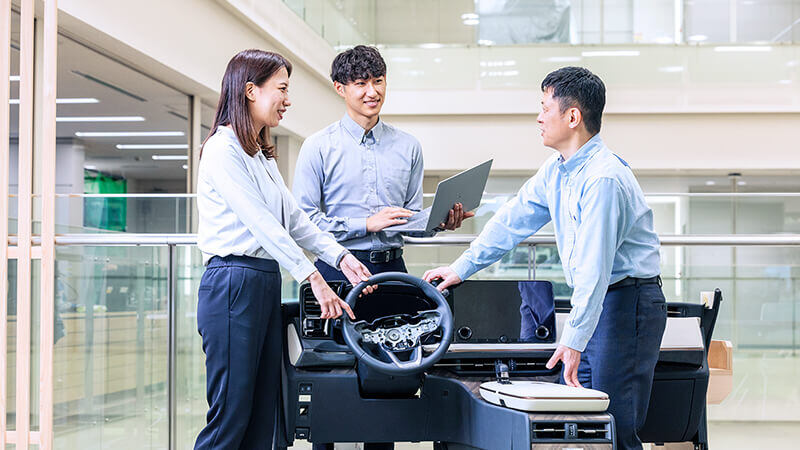
クルマの安全性や機能性をつかさどる細かい部品まで、設計データをつくります。それらをもとに、協力会社と協力して各部品を開発・製造し、試作車をつくります。
実験・評価
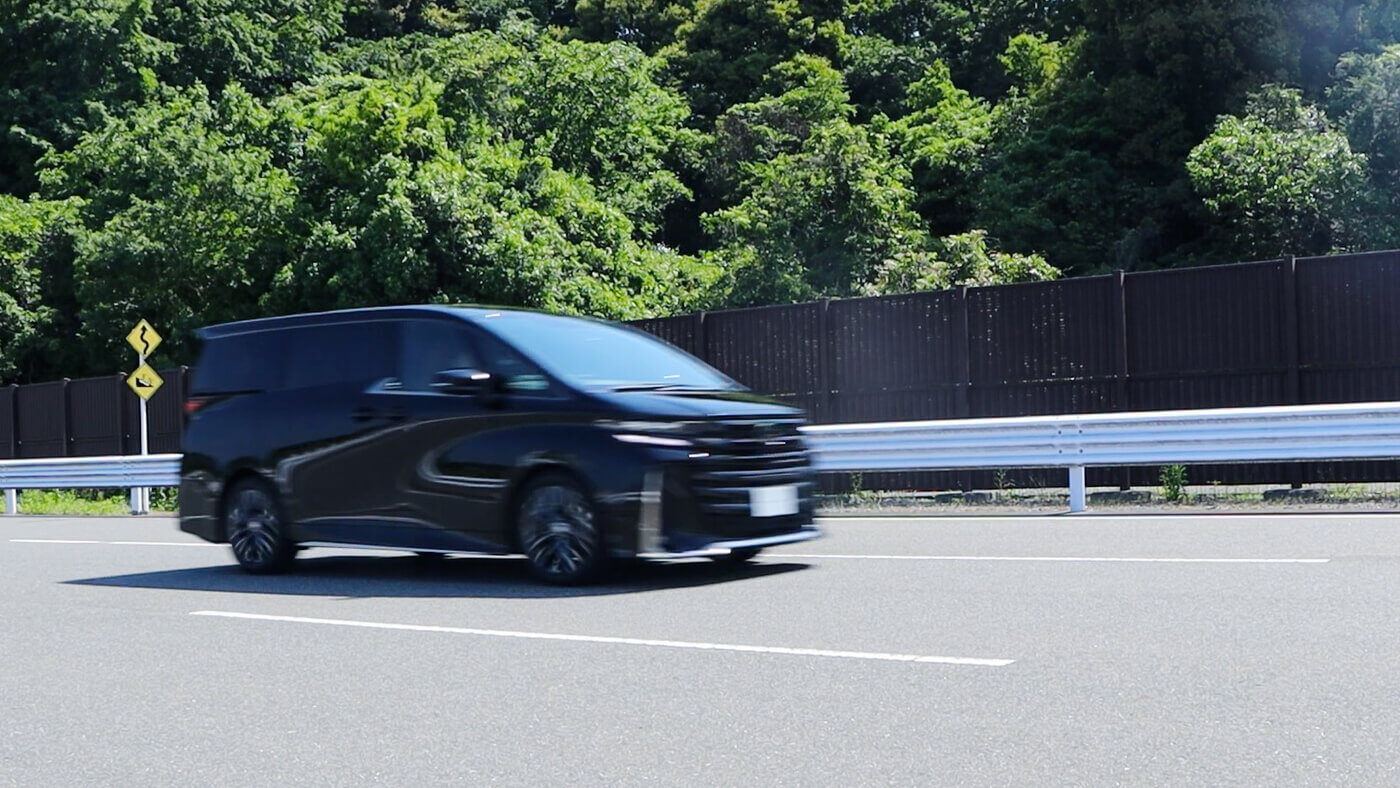
車両にまつわる性能をさまざまな厳しいテストを行い評価します。
あらゆる路面における悪路走破性能、安全性能、開閉耐久性など細かいテストを何度も繰り返します。
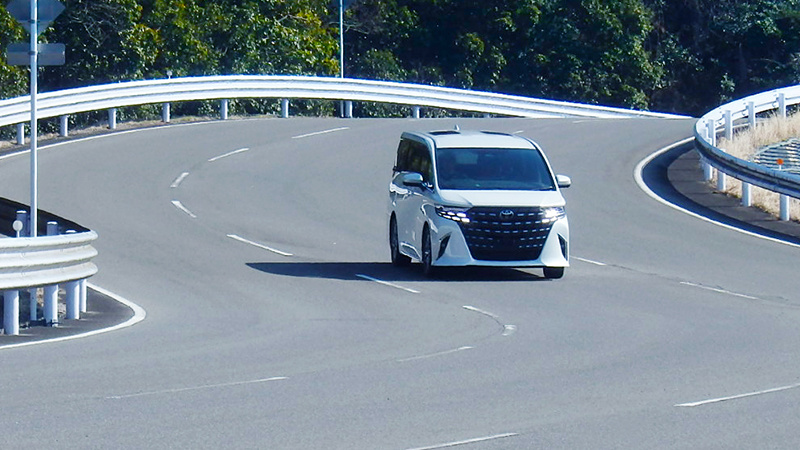
世界各地の道路や天候、気象を想定したテストを行います。次にテストで得られた結果をもとに、試作車の設計を見直し、改良し、再びテストを行います。
データだけでなく、人の感覚も大切にし、テストを何回もくり返して、お客様の期待を超えたクルマをつくりだします。
生産準備
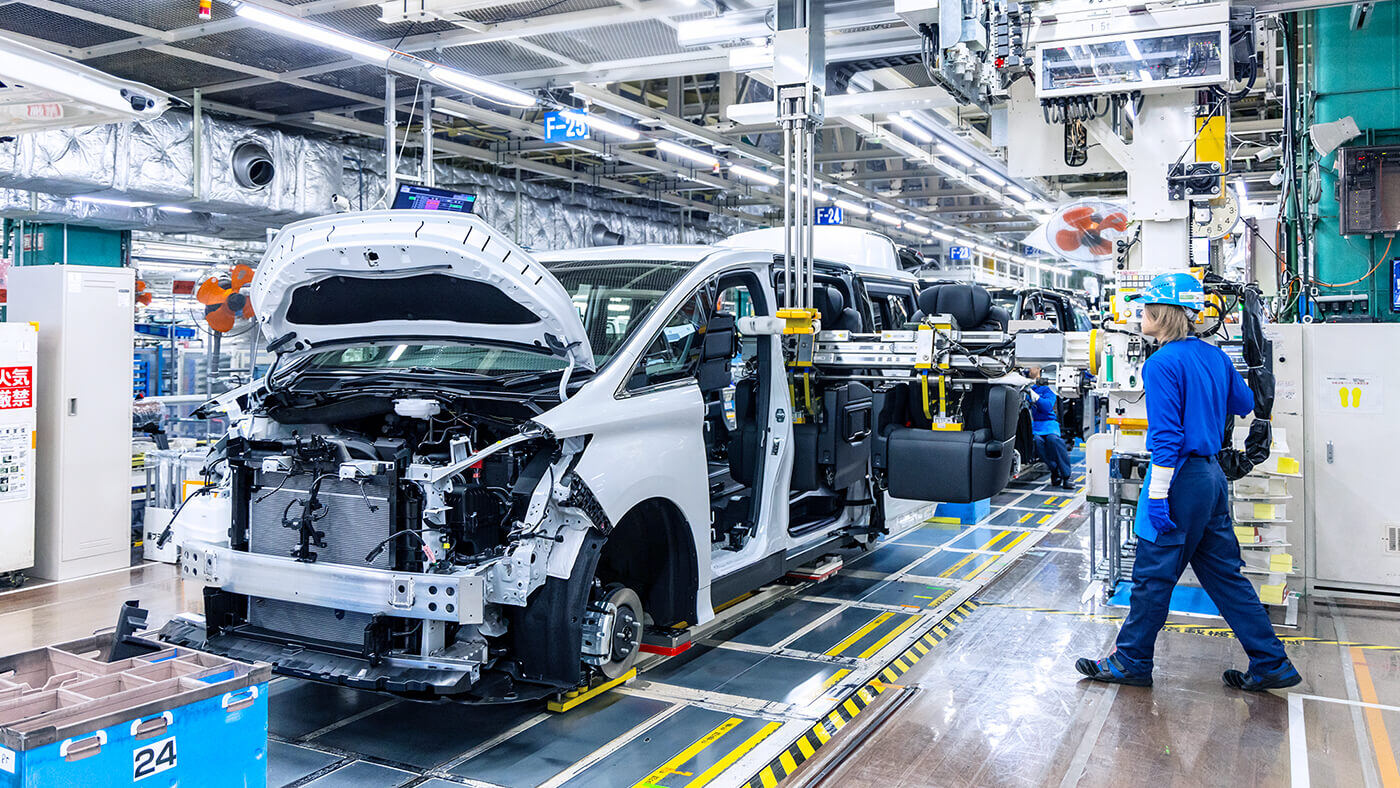
「人にやさしい工程づくり」「人が主役の道具づくり」「変動へのスピーディな対応」の実現に向け、TPS(Toyota Production System)を中心とした生産ラインの改善を推進。
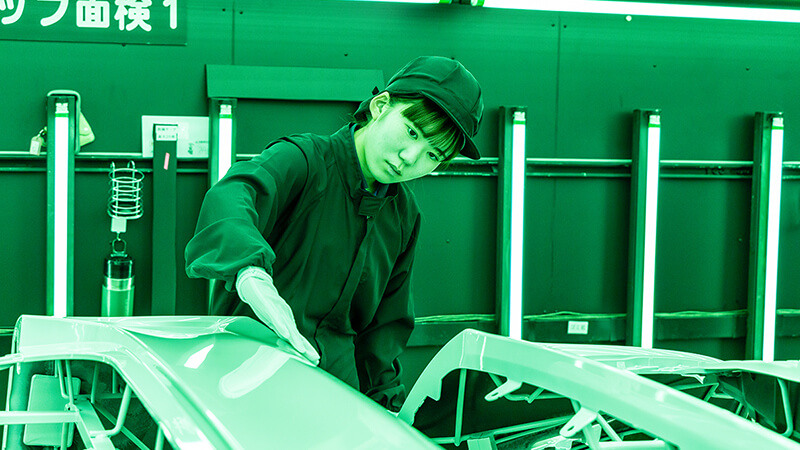
人にやさしい工程づくり
重いものを持たない、負担のかからない作業姿勢を検討したり、安全で、すべての人が仕事しやすく、確実に作業に取り組める工程づくりを工場と生産技術が徹底的に追求しています。
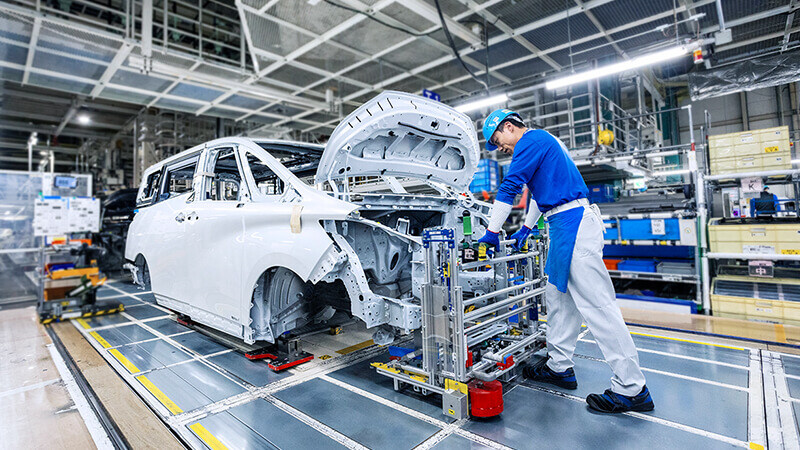
人が主役の道具づくり
万が一、人が操作を誤っても安全や品質が確保できるFP(Fool Proof)装置や組立順序に従った部品供給システム(順建て)を生産ラインの随所に導入。現場の知恵を生かして、働きやすさ、品質向上の観点で思いついたアイデアを会社に提案する「創意くふう提案制度」など自らの工夫による改善も積極的に進めています。
生産
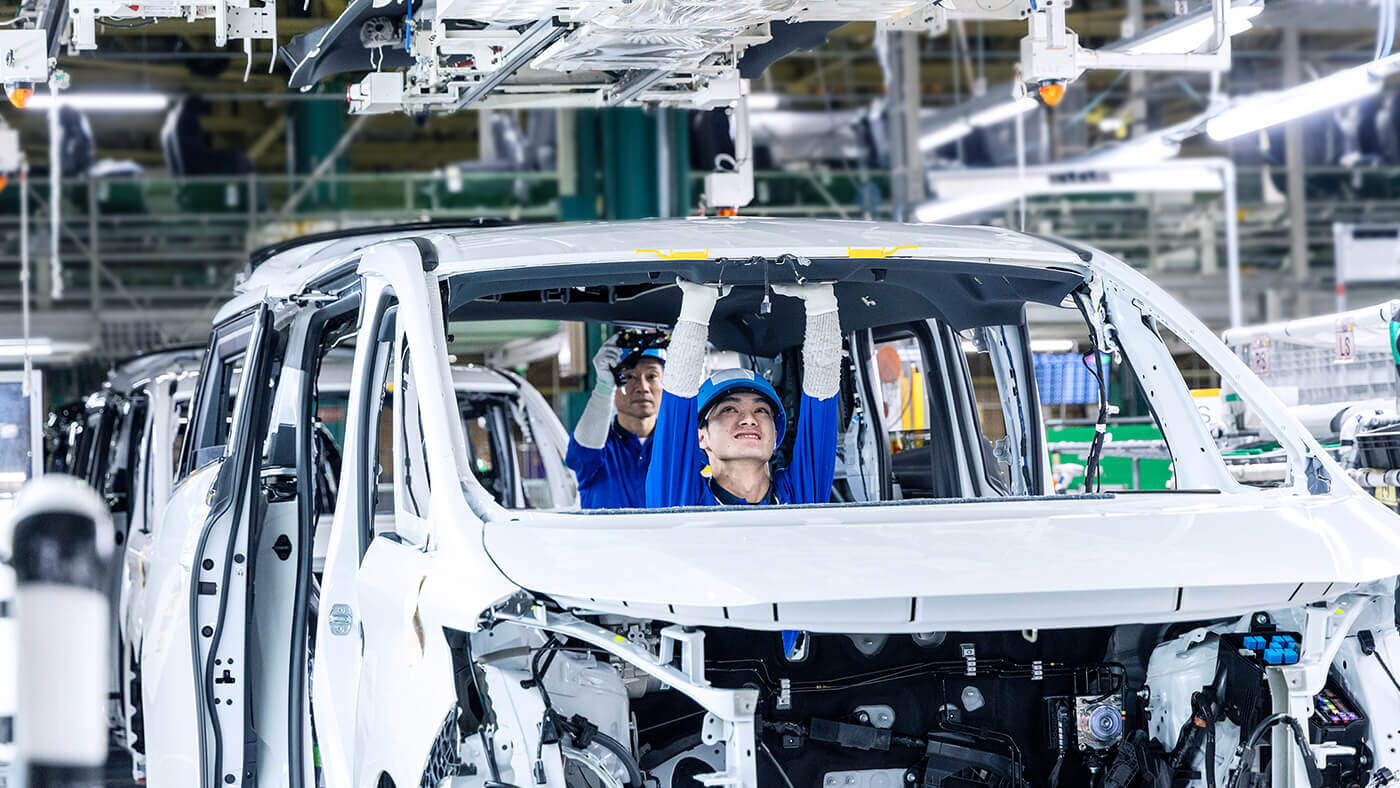
決定したデザインや機能に基づきクルマをつくっていきます。
ボデーをつくり、塗装し、各部品が順次取り付けられ、クルマの形が完成します。組立後、詳細に品質検査が行われ、完成したクルマは出荷されます。
プレス工程
業界でも最大クラスの大型プレス機によって、車体やドア、天井などクルマを構成する部品をつくっています。
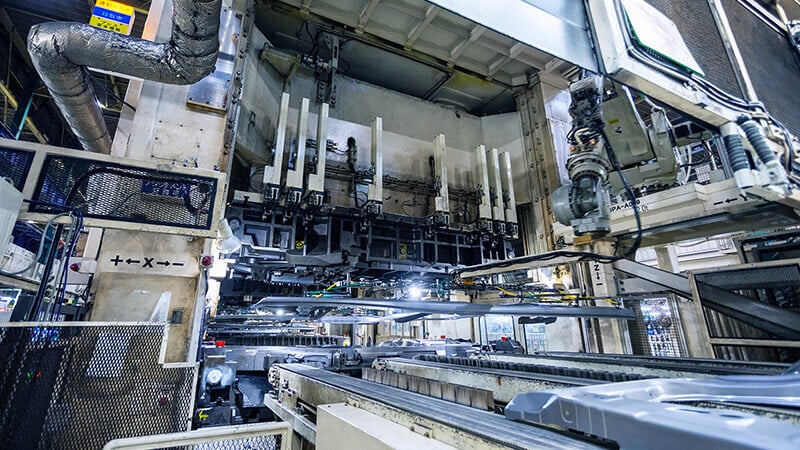
溶接工程
プレス工程でつくられたさまざまな部品を、ロボットをつかって熱で鉄板どうしを溶かしてつなぎ合わせ、クルマの形をつくります。
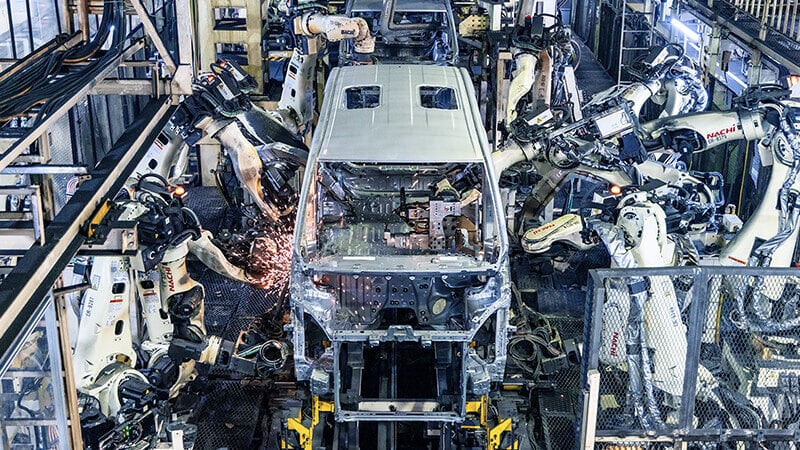
塗装工程
クルマの形になった車体を、環境にやさしい水性塗料をつかい、塗料を塗っていきます。クルマの美しいツヤを出すために4回塗り重ねていきます。
最先端の環境に配慮した設備を導入しています。
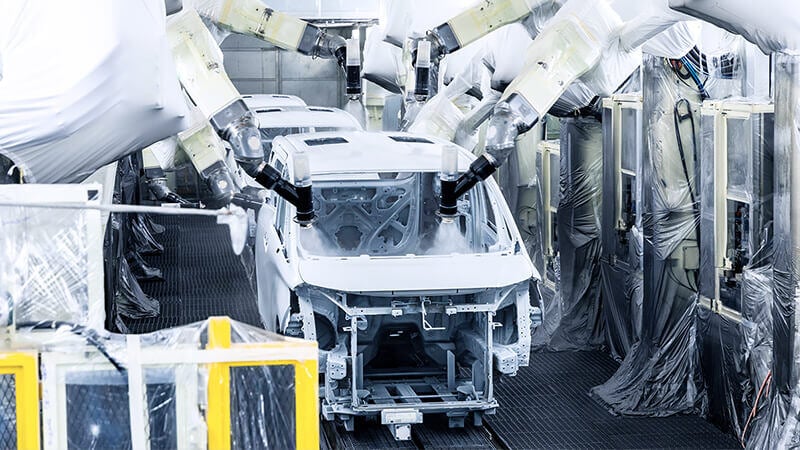
組立工程
塗装した車体にさまざまな部品を取り付けていきます。
組立工程では一定の速度で動くコンベアの上に車体をのせて、多くの作業者の手によって、部品を正確に取り付けていきます。
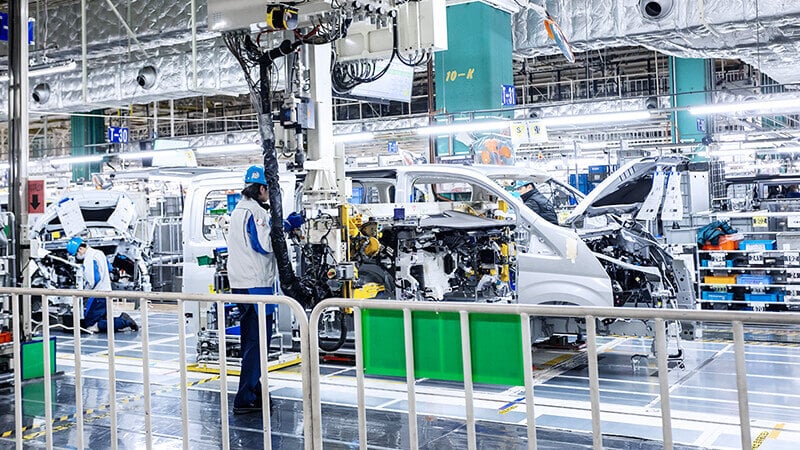
検査工程
お客様に安心、安全に乗っていただくため、完成したクルマを人と機械で細かくチェック。法規に適合した検査を行っています。
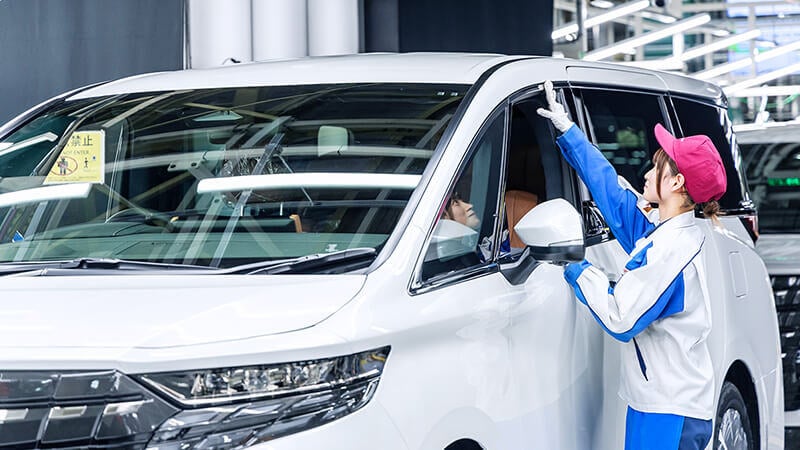
出荷
厳しい検査に合格したクルマは、工場から出て、世界中の販売店やお客様のもとに届けられます。
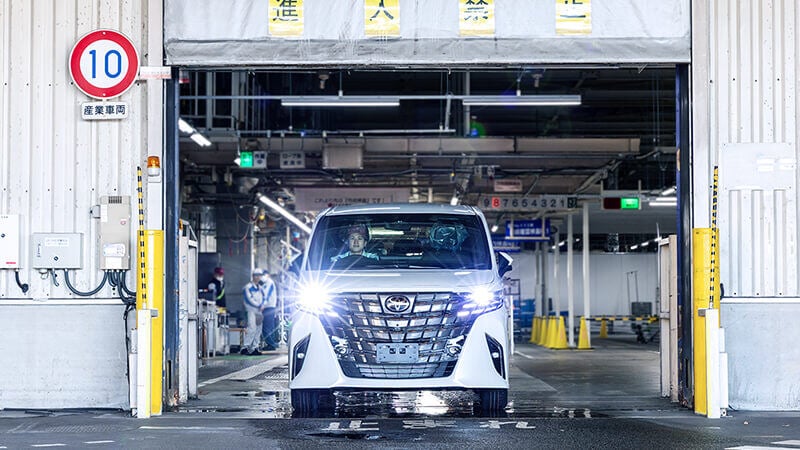